Vacuum Equipment and ATV Equipment
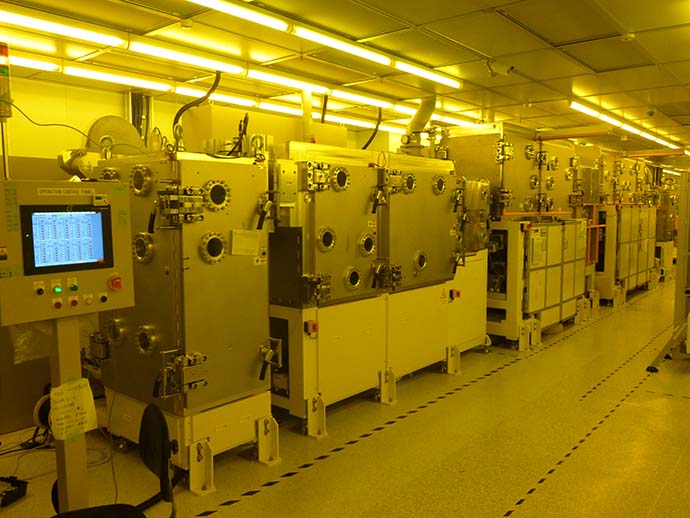
Kanadevia provides various deposition equipment and related equipment for organic EL lighting and functional film formation. We support various base materials such as films, glass, and wafers. We also respond to a wide variety of requests from cluster type to roll-to-roll type, and from experimental machines to mass production machines.
Additionally, we also have ATV (Air to Vacuum) equipment to transport the film continuously from atmospheric environment to the vacuum.
Major products
Surface evaporation source
Features
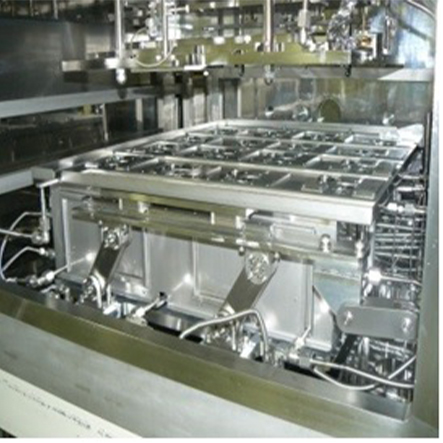
The deposition rate is stabilized through optimal nozzle arrangement and valve control. This achieves high in-plane uniformity and highly-efficient utilization of material despite the formation of static film.
Moreover, it is possible to perform co-deposition for up to three sources and deposition of inclined film.
- <Main specifications>
- Maximum base size: G6 base(1,500×1,850mm)
- Uniform film thickness ≤ ± 3% (± 2% is also possible)
- Continuous maximum usage temperature: 400℃
- Maximum number of installed sources: 3 sources (supports co-deposition)
- Deposition rate measurement QCM, pressure rate sensor
- Deposition rate control: Controlled by crucible temperature and valve opening for deposition
- Crucible position: Located outside of vacuum chamber
- Material filling: Deposition material can be replaced without exposing the chamber to the atmosphere
- <Examples of practical use>
- Organic film evaporation source for clustered organic EL lighting
Nozzle linear source
Features
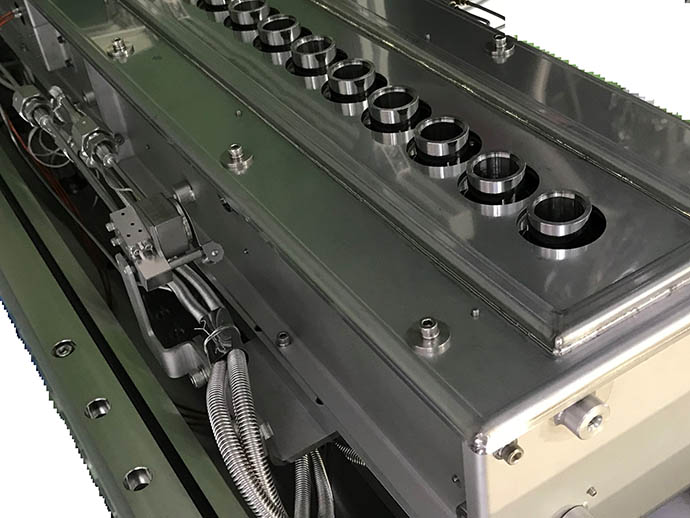
Kanadevia has achieved commercialization based on technology cultivated in our development of surface evaporation sources. There is a high degree of design freedom and the deposition direction is not limited. A solvent removal function for liquid materials can be also be added.
- <Main specifications>
- Maximum base width: 2,000 mm
- Film thickness uniformity in width direction: ≤ ± 3%
- Continuous maximum usage temperature: 400℃
- Maximum number of installed sources: 3 sources (supports co-deposition)
- Deposition rate measurement QCM, pressure rate sensor
- Deposition rate control: Controlled by crucible temperature and valve opening for deposition
- Crucible position: Located outside of vacuum chamber
- Material filling: Switching mechanism for crucible materials (optional)
- <Examples of practical use>
- Evaporation source for in-line equipment
- Evaporation source for roll-to-roll film film formation
Damageless EB evaporation source
Features
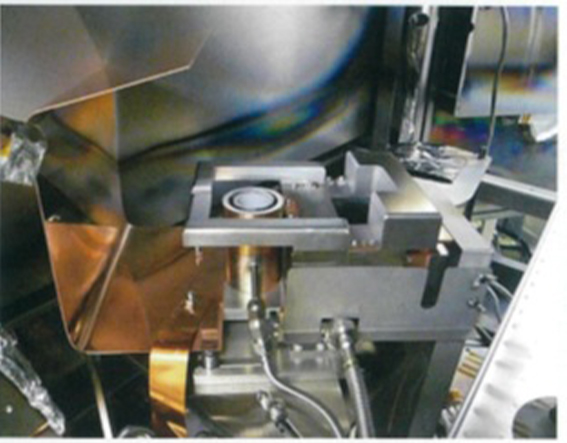
This evaporation source forms metal materials and inorganic materials on organic film in organic devices. The equipment uses a low X-ray dose and a proprietary backscattered electron trap. The heat insulation of the crucible enables high-speed film formation at low frequencies. This makes it possible to obtain element characteristics comparable to those of conventional resistance heating.
Additionally, by combining an automatic supply mechanism for materials, the equipment achieves continuous film formation for 100 hours.
- <Examples of practical use>
- Metallic film evaporation source for clustered organic EL equipment
- Evaporation source for roll-to-roll film film formation
Rotary cathode
Features
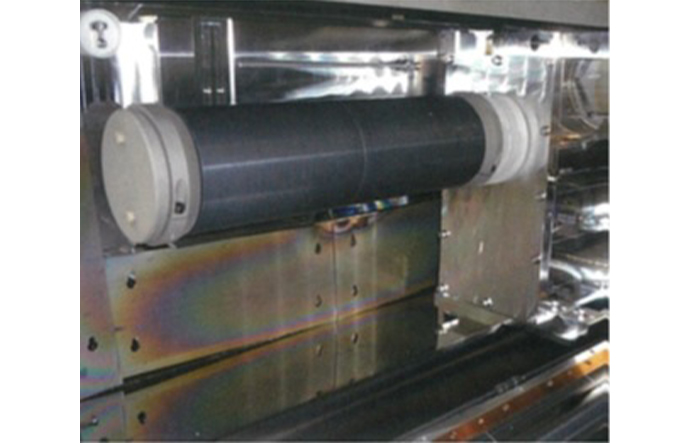
The high efficiency of material utilization reduces the frequency of target replacement, and the high cooling effect enables high-speed film formation.
- A longer lifespan is achieved by strengthening the vacuum seal (increased from 1 year to 5 years)
- Realization of large flow rate of cooling water required for high-speed sputtering (100ℓ/min)
- End blocks are designed in-house, and magnets are designed and measured in-house
- <Examples of practical use>
- Cathode for roll-to-roll film film formation
ATV (Air to Vacuum) equipment
Features
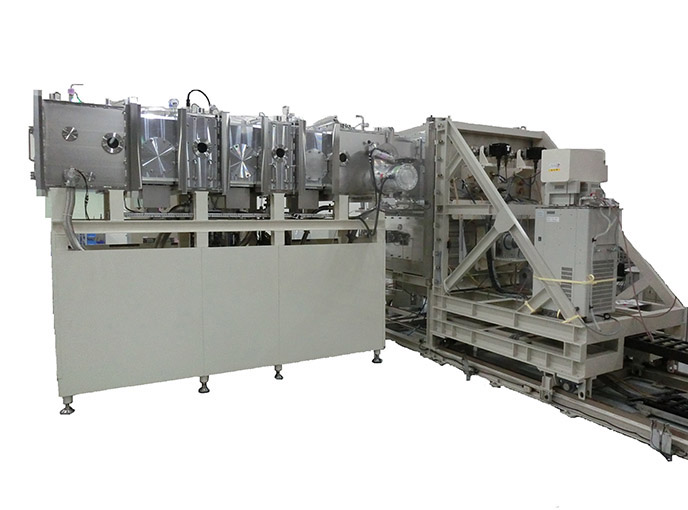
Our proprietarily developed ATV mechanism realizes continuous transfer of film from the outside atmosphere to the vacuum. (It can also be used for differential pressure control in different vacuum regions.) This mechanism maintains a high operating rate of vacuum equipment and greatly contributes to productivity improvement.
Design specifications (separate consultation) | Experimental machine specifications | |
---|---|---|
Web speed | MAX 30m/min | 0.5~10m/min |
Film width | MAX 2,000mm | 300~500mm |
Film thickness | MAX 200µm | 25µm~200µm |
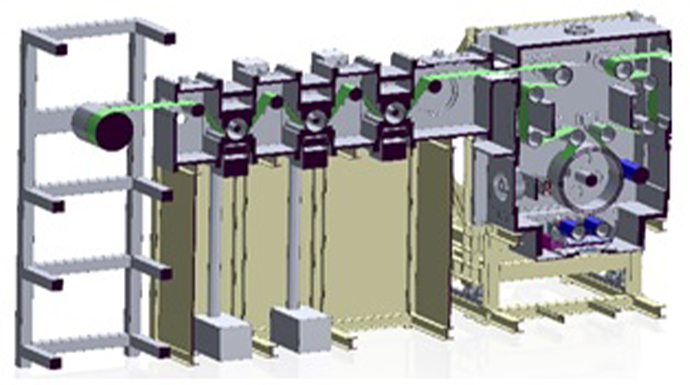
Related technology
Click here for inquiries about Kanadevia technology