Marine Civil Engineering
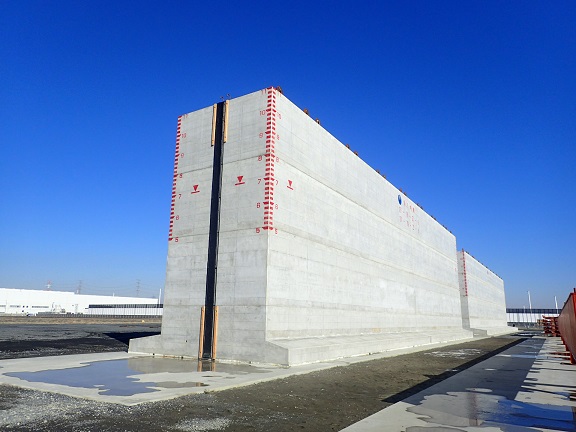
We have participated in many ocean civil engineering projects and provided many products relating to harbor equipment and improvement of fishery harbors and fishing grounds, including large floating structures (bridges on the sea). Along the way, we have accumulated advanced technological know-how and developed futuristic technologies. Expanding the available area for life and increasing the diversity of spaces on and under the sea is expected in the future and the possibilities are limitless. We will further pursue the creation of an ocean space solution that makes the impossible possible.
Major products
Immersed tunnels
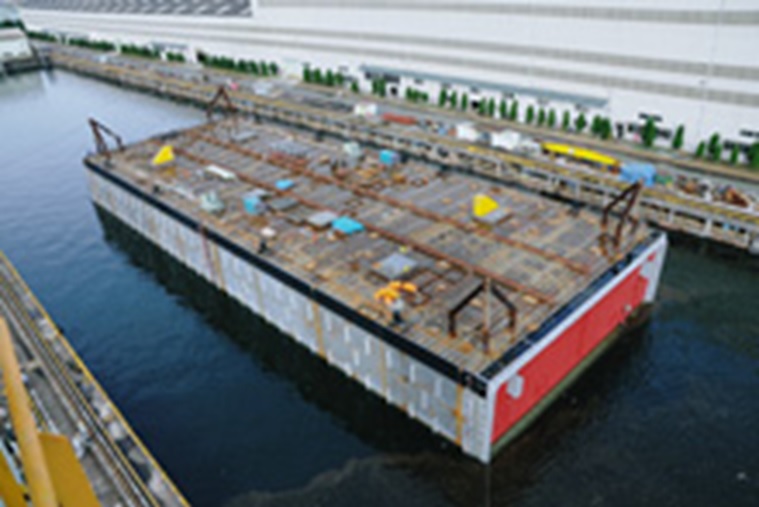
An undersea tunnel is a large hybrid structure of steel and concrete formed on the sea bed via the valley filling method. The structures are built at the Sakai Works No. 2 and No. 3 docks. This involves fabrication of the steel shell blocks, assembly, and concrete pouring. For tunnel lengths of 100 meters, three sections can be built simultaneously. The No. 2 dock can accommodate longer tunnel shells of up to 170 meters in length. Kanadevia has built over 40 undersea tunnels including those at the Osakako-Sakishima tunnel, the Osakako-Yumesaki tunnel, the Kobeko-Minatojima tunnel, and on the Nahako-Rinkai road (Port of Naha harbor road) and the Shin-Wakato road immersed tunnel.
Major achievements in recent years
- Manufacturing/construction for New Wakato Tunnel (Section No. 7) (2009)
- Manufacturing/construction for New Wakato Tunnel (Section No. 6) (2010)
- Port of Tokyo, Bay Port Road, Namboku Line (Section No. 1, 2, 3, 4, 5, and 7) (2017)
Hybrid caissons
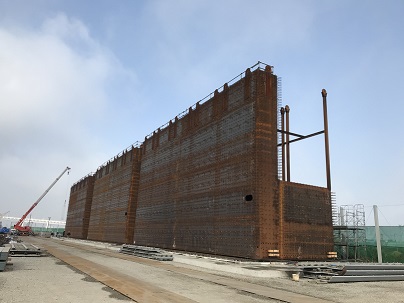
Hybrid caissons, which consist of a steel structure and concrete, are often used for bank protection and pier facilities in ports and fishery harbors. In addition to the key role as a breakwater, we are developing a new environmentally sensitive type of caisson that promotes seawater exchange using the energy of waves to restore and preserve the coastal environment as well as slit caissons that have a wave-absorbing effect.
Recent construction results
- Misaki Specified Fishing Port Development Project (2007)
- Futamachiya-Nishi Coastal Levee Construction (Stage 2, 2008)
- Manufacturing/construction for Harumi 4-chome Seawall Caisson (2011)
- Outer Revetment Construction at Sediment Disposal Site, Shinnanyo District of Tokuyama-Kudamatsu Port (2012)
- Manufacturing/construction for C Revetment Caisson at Ukishima Term 2 Waste Landfill and Disposal Site (2012)
- Manufacturing/construction for caisson at Hitachinaka Next Disposal Site (2015)
- Manufacturing/construction for tide embankment at North Port District, Wakayama-Shimotsu Port (2019)
- Manufacturing/construction for caisson steel shell during construction of Shinhonmoku pier (2020)
Floating structures
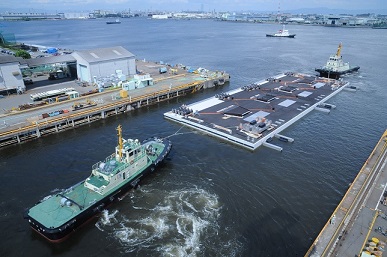
Floating bridges are designed to accommodate tidal movements and are commonly installed at harbors and fishing ports. Kanadevia has constructed over 60 floating bridges, starting with the first steel floating bridge built in the early Showa Era (1926 - 1989).
Major achievements in recent years
- Manufacturing/installation of a floating pier for Wide Area Fishing Port Development Project at Toushi Port (2006)
- Manufacturing/installation of a floating pier at Tokujin Port, Okinawa Prefecture (2007)
- Manufacturing/installation of a floating pier at Kanokawa Port (Ohara district), Hiroshima Prefecture (2007)
- Manufacturing/installation of the Miyajimaguchi floating pier, Hiroshima Prefecture (2015)
Steel jackets
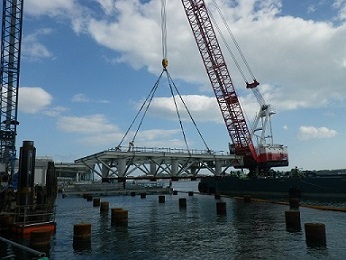
The jacket method is being adopted in many cases for bridges and bank protection in freight container terminals. It involves the manufacture of jacket superstructures of a steel pipe truss structure on land (i.e., at the factory), which are then carried to the building site and mounted on base piles. The jackets have superior earthquake-proof features and the method is attracting attention as an earthquake-proof-enhancing pier construction method because it can be built on soft ground and in the deep sea. The bridge at the south district pier (-16 m) in North Osaka Port adopted this method and two jackets for it were manufactured at our Sakai Works.
Major achievements in recent years
- Manufacturing of No. 6/7 Jacket at Yumeshima (West Side) (2008)
- Manufacturing/installation of jacket at Fukuyama Port (Minooki District 21-4) (2010)
- Disaster recovery work (Stage 1) and manufacturing/installation of jacket for fish market pier, Shiogama Fishing Port (Outside Superstructure) (2014)
- Disaster recovery work (Stage 2) and manufacturing/installation of jacket for fish market pier, Shiogama Fishing Port (Outside Superstructure) (2017)
- Manufacturing/installation of jacket for construction at outer facility of Ichikawa Fishing Port (2017)
Steel plate cells
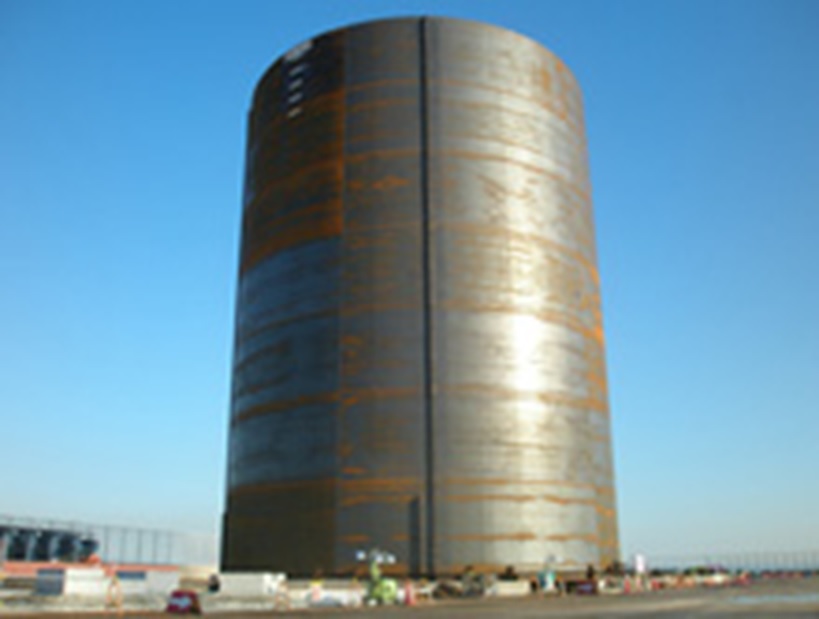
Steel plate cell installed in revetment area
The setting depth steel plate cell method, a construction technique for landfill bank protection, involves hammering steel cylinders called cells (which are produced onsite) into the seabed then filling the cells with earth and sand. This form of protection is superior in terms of its earthquake and waterproofing features, and has been the focus of attention as a suitable construction method for bank protection in the deep sea and for quick construction. Steel plate cells are built on site at the yard from steel materials that are assembled as panels via welding. We have built over 100 steel plate cells to date.
Recent construction results
- Construction for revetment at Osaka Bay Offshore Landfill Disposal Site (18.5 meters in diameter × 16 meters high × 26 units)
- Construction (Phase 12) for seawall at Kansai International Airport island (Stage 2) (22 meters in diameter × 24 meters high × 8 units)
- Landfill seismic revetment in Minami-Honmoku District, Yokohama (24.5 meters in diameter × 32 meters high × 6 units)
- Manufacturing of steel plate cell for landfill revetment in Hitachinaka Port District (21 meters in diameter × 21 to 26 meters high × 72 units)
Steel fish reefs
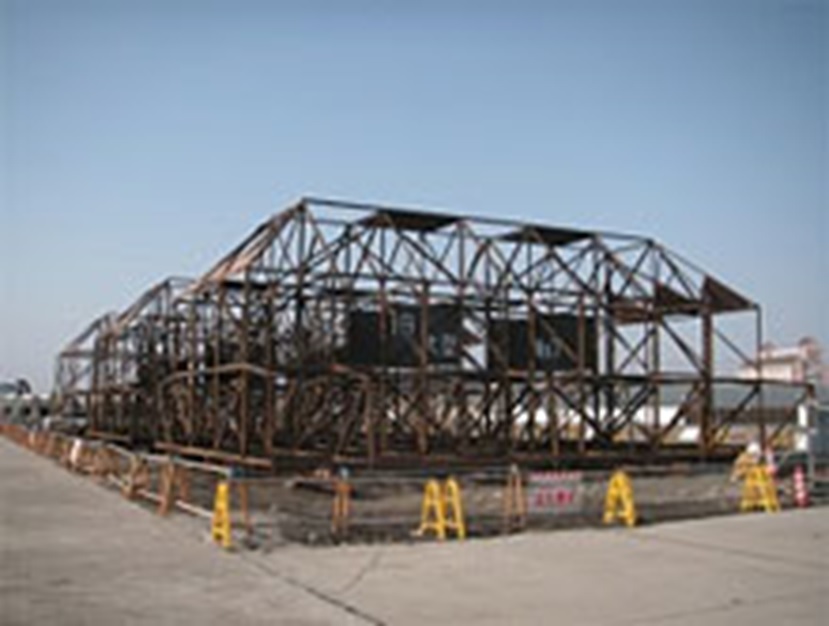
Steel fish reefs are steel frameworks that are placed on the sea bed at fisheries to provide fish with a ready-made breeding habitat. Kanadevia has built over 330 artificial reefs since the first was installed in 1975. The reefs employ a convex shape that is designed to prevent fish nets from becoming entangled.
For maximum quality and minimum construction period, steel fish reefs are assembled as blocks. Kanadevia offers a choice of four models: the HZ-300NB, 400NB, 500NB and 1200NB.
Major achievements in recent years
- Installation/construction for Kurosaki Offshore Parallel Underwater Reef in Miyazu City, Kyoto Prefecture (2008)
- Construction of large underwater reef in Hirakata-Otsu District (2008)
Related technology
Click here for inquiries about Kanadevia technology